The cleanliness department here at Particle Technology have recently begun realigning many of our internal testing procedures in cooperation with UKAS 17025 accredited ISO 16232:2018 specifications for the cleanliness testing on automotive components.
Our internal TM101 testing procedure typically involves testing inside an enclosed cleanliness rig, located inside a specialised HEPA room.
A High-Efficiency Particulate Air room (HEPA) is a specifically designed environment that utilises high efficiency particulate air filtration to maintain a clean and contaminant free space where strict air quality standards are essential.
The key features of a HEPA room is the filtration system, with filters capable of removing airborne particles as small as 0.3 micrometres with a near 100% efficiency rate, meaning our large parts testing capabilities are of the highest industry standards.
Cleanliness Testing of Large Components to Improve Performance
The primary focus of large parts testing is to evaluate the level of cleanliness and the absence of contaminants on large components or structures.
Large parts cleanliness testing is particularly important in the automotive and aerospace industries where even the smallest contaminant particles can have a detrimental effect on performance, reliability and safety of the final product.
As one part of Particle Technology’s wide range of available testing capabilities, we are often required to test parts that are greater than 45kg.
When testing larger or heavy components a different process must be adopted.
The continued development of our testing procedure has focused on areas of improvement which involve designing and manufacturing dedicated areas for the use of large components testing equipped with lifting cranes and eye bolts to hold large components over a dedicated collection basin.
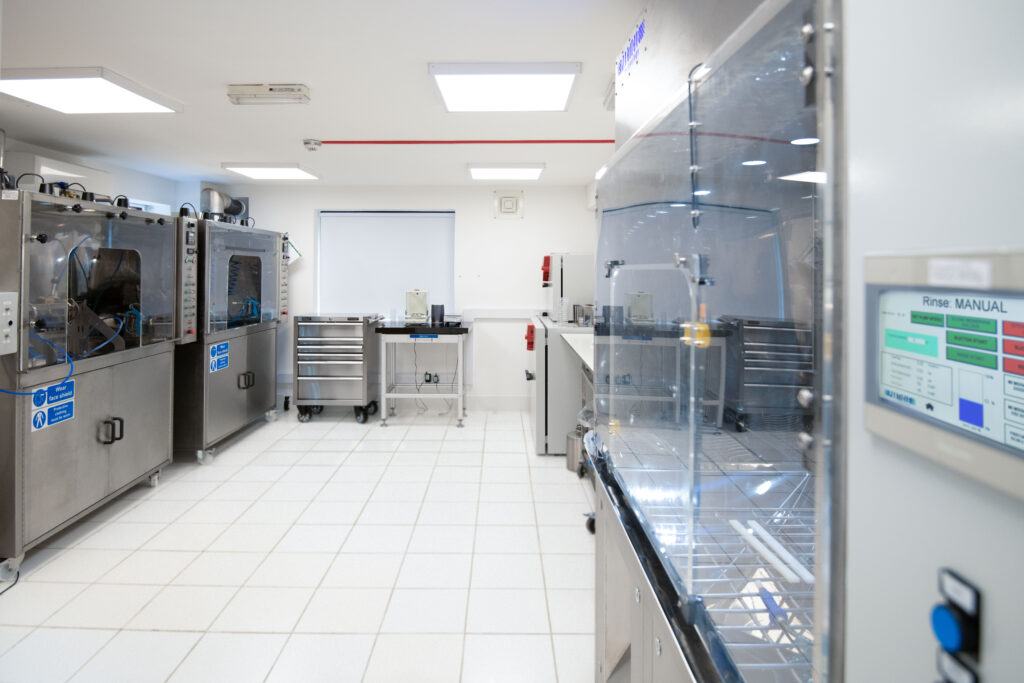
Large Engine Block Study
To further validate the effectiveness of our large part testing procedure, our cleanliness department conducted a study by using our large parts cleanliness testing equipment on a large engine block.
This thorough testing process involved targeting different test locations such as high and low pressure oil, as well as water gallery locations.
In order to successfully attach the engine block onto an engine, a specially designed adaptor plate was designed and manufactured to assist with the test process.
A number of other components have since been successfully tested using this collection basin and equipment after which the equipment is cleaned to desired blank limits ensuring validity of future tests.
Through this study we were able to conclude that our updated large part testing procedure and equipment had been successfully manufactured and would continue to meet ISO 16232:2018 specifications.
Cleanliness Testing From Particle Technology
Through our innovative new procedures in accordance with the latest TM101 procedures, we are able to improve the cleanliness levels of components in a range of sizes, helping to enhance product quality, lifespan, and overall customer satisfaction.
If you would like any more information about Cleanliness Testing or other services and products from Particle Technology, please browse our website or get in touch today.